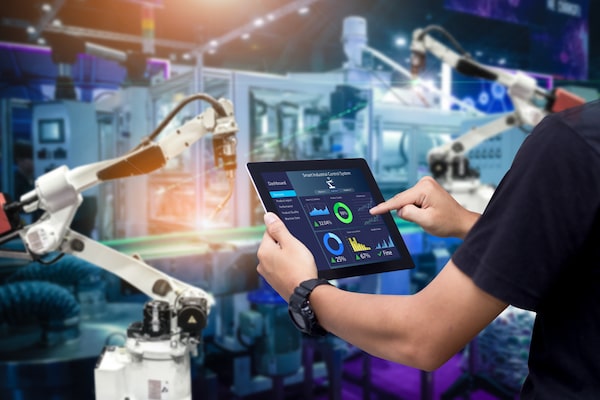
Industry 4.0 imagines a digitally connected shop floor where a constant flow of information between machines and workers automates and optimizes production.PANUWAT/iStockPhoto / Getty Images
Revolutions often don’t happen overnight.
In 2015, economist Klaus Schwab first described an emerging “fourth industrial revolution,” referring to how new technologies such as artificial intelligence, mobile communications devices and the Internet of Things were transforming industry and manufacturing.
Also called Industry 4.0, its most potent expression can be found in the Smart Factory concept – a digitally connected shop floor where a constant flow of information between machines and workers automates and optimizes production, tracks inventory and keeps real-time data on maintenance and other needs. Ultimately, the data will extend outside the factory, connecting to supply-chain planning and beyond.
But Industry 4.0 has a few prerequisites. More than anything else, it requires fast, reliable wireless connection between devices, sensors and computers, able to deal with industrial-scale data volumes. That’s where the revolution has been slower to take hold – and where the promise of 5G looms so large.
“5G is not just an incremental improvement over LTE and 4G, but really something transformative,” says Robert Barton, a Cisco Canada distinguished systems engineer. “It will allow things to be done that would otherwise be impossible.”
While 5G technology is still rare on factory floors, there are plenty of industry leaders paving the way for its adoption. Among them are those found in the Global Lighthouse Network, a “community” of 44 manufacturing facilities recognized by the World Economic Forum that are considered Industry 4.0 leaders. They range from a Hitachi plant in Japan to a Nokia factory in Finland, which uses a private, in-house wireless network to connect its robotics.
There are no lighthouses yet in Canada, but there are a growing number of domestic Canadian Industry 4.0 leaders.
This February, aerospace manufacturer Lauak Canada announced it would transform its factory in Mirabel, Que., into a high-tech aeronautics centre centred on Industry 4.0 principles. And in 2016, General Electric one-upped the smart-factory concept, breaking ground on a “brilliant” factory in Welland, Ont. The facility, which manufactures industrial gas engines, streams data from machine-embedded sensors into a cloud-based analytics program and returns suggestions to engineers on improving operations. (The factory was sold in 2018 after the GE division it was part of was acquired, but continues to operate.)
Mr. Barton says these kinds of outfits will be the first to derive the benefits of 5G, but others will quickly follow. Those benefits include ultra-high bandwidth (up to two gigabits per second) as well as ultra-low latency, the time it takes for a signal to travel between end points. That can be as much as 20-to-30 milliseconds on a 4G or LTE network and as little as one millisecond on 5G.
When 5G-enabled manufacturing facilities are rolled out, Mr. Barton says that latency advantage in particular will be pivotal.
“Let’s say you have a machine that once an hour sends a temperature update,” Mr. Barton says. “That can operate on WiFi, because it’s low priority, and if it’s delayed or slowed down, it’s not a big deal. On the other hand, if a self-driving dolly is zipping around a factory floor, that link has to be maintained without any interruption, or the dolly could crash. So that would be on 5G. Meanwhile, workers on their phones could be on 4G.”
At the same time, machinery and robots outfitted with 5G sensors will also be able to provide an enormous, steady stream of information about performance and wear-and-tear, allowing manufacturers to move from expensive, episodic repairs to predictive maintenance.
“That’s really important because downtime is hugely costly, one of the greatest expenses any manufacturer has,” explains Dennis Darby, president and CEO of Canadian Manufacturers and Exporters (CME). “A faster transfer of data will allow for sensors that can track performance in real time, and that means problems can be dealt with before they become breakdowns.”
Finally, 5G may open up new possibilities to reprogram and repurpose machinery, allowing factory robotics to be reprogrammed remotely, from anywhere in the world, rather than requiring teams of engineers to visit each facility in need of retooling.
A nationwide 5G rollout is yet to come since the federal government hasn’t finished allocating space on the domestic radio spectrum to 5G providers.
But that holdup doesn’t impede manufacturers that aim to establish private 5G networks within individual facilities, says Duncan Stewart, director of technology, media and telecommunications research for Deloitte Canada.
“I’d expect to see any number of private Canadian 5G networks and trials within the year,” Mr. Stewart says. “Especially among logistics and distributions outfits.”
Cellular 5G will be necessary, however, to transform supply chains.
“When that comes, we’ll see an avalanche of 5G IoT devices in shipping, receiving and ports,” Mr. Barton of Cisco Canada says. “That will enable visibility right up the supply chain.”
By visibility, Mr. Barton means exactly that – an unprecedented ability to track goods as they move through the supply chain: tracking where raw materials are, when inventory is shipped, where it may be held up and its condition.
Mr. Barton uses the example of a food retailer using environmental monitoring sensors to track food spoilage in a truck or rail car. It will also, he points out, help create a more accurate picture of what the industry terms “shrinkage” (i.e. theft).
The challenge in Canada, according to the CME’s Mr. Darby, is adoption.
“We are behind in Canada relative to many other countries we compete with,” he says. “We don’t want to miss this next generation of change.”
That goes not just for national 5G infrastructure, but for private networks as well. Mr. Darby says Canadian manufacturers have been slower on the uptake to embrace Industry 4.0 principles, compared to international competitors.
Nonetheless, those changes are coming.
“This is technology we’ll be deploying over the next decade, Mr. Stewart of Deloitte says. “Whether we’re six or nine months behind is not necessarily material – this will be a marathon, not a sprint.”